OMC Prices, Functions, *Features
($0 / year)
Manage up to 30 Equipment Items
Unlimited users
Minimum 5 users ($120 / year)
Manage up to 75 Equipment Items
Unlimited users
Minimum 6 users ($360 / year)
Manage unlimited Equipment Items
Unlimited users
nb: All versions of OMC software; OMC-Free, OMC-Express, and OMC-Professional are identical except for the limit on the number of Equipment that the maintenance program can track and manage.
OMC – Block Diagram and Features
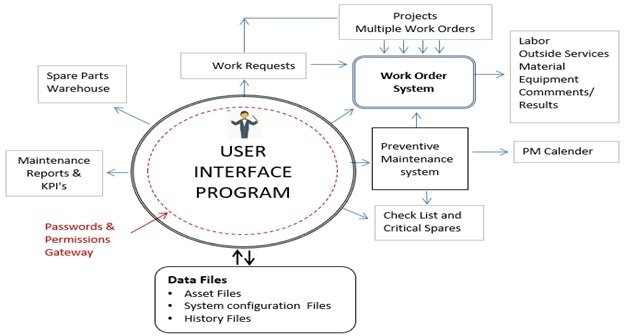
Equipment Data Files – A set of
Data files that store the Equipment information at your facility.
Stores Equipment Data, such as Name, Number, Location, Maintenance Supervisor, Type, Classification, Maintenance Checklist, critical spares, Maintenance frequencies, Criticality and Parent-Child relationships.
Optional Data that may also be stored includes nameplate information, Warranties, Valuation data, Purchase dates, Service life and residual life data.
Work Request Function – A system that tracks and records all request for Maintenance work.
- Create and Route Work Request to the Maintenance Department
- Convert Work Requests to Work Orders
- Convert a Work Requests to a Project
- Link Work Request closure to Work Order closure
- Track Work Request by Employee, Location, Equipment, Priority, Category or completion status
- Add progress milestones and comments to work requests.
- Print , Preview or Mail Work Requests
Maintenance Planning Calenders – Two independent PM planning calenders that preview’s upcoming PM jobs for any period into the future. This first calender is organized by Month, and the second is organized by Equipment.
Create, Print , Preview or Email color coded PM Calendars that show upcoming PM jobs for any period into the future on two separate Calenders. Use the Calenders to:
· Identify and Analyze resource constraints or bottlenecks.
· Reschedule around weekends or public holidays.
· Manage PM jobs that have multiple PM frequencies,
· Fine tune PM plans before creating the PM work orders.
· Get excellent visibility along the planning horizon, and make the changes needed to optimize maintenance plans
Additional Features and Functions
Fault codes – Assign Fault codes to failures types, to gain insights into failure patterns and improve root cause analysis
Projects Function: A system that groups and tracks multiple work orders under a single named collection called a Project.
Spare Parts Warehouse Function: Optional module to track spare parts Received, Issued, reserved, Used, Returned, Inventory, Negative issues, and Usage.
Warehouse reports include, Inventory transactions, Min max levels, low inventory levels, reorder quantities and stock on hand.
Password and Security Function
· Accepts five (5) different categories of users from Guests to the CMMS Administrator, with each category (group) having its own permission settings. Types of permission settings are: no access, read only, read and write and read write and delete access.
· Requires each user to have a login password.
· The Password function can be disabled by the CMMS Admin.
Preventive Maintenance Function – A system that tracks and manually or automatically schedules equipment that are due for time based periodic Preventive Maintenance.
- Manual of Automatic PM scheduling for time based frequencies in days
- Preview, print or mail list of upcoming PM jobs for any period into the future.
- Manual triggering of meter based PM’s
- Create and store PM Work orders based on user configured settings.
- Create PM work orders based for selected criteria such as location, supervisor, date range, or Parent.
- Print a checklist for each scheduled equipment (optional)
- Assign PM due date based on fixed days or % of maintenance frequency
Multiple PM Frequencies per Entity or Equipment
- Track up to 4 independent time based frequencies (example, 1mth, 3mth 6mth 1yr)
- Track up to 2 independent meter based frequencies (example 300hrs, 1000 hrs) for each
Equipment PM CheckList
- Create and store multiple frequency check list in the check list library.
- Link (associate) a check list to any Equipment or Entity
Work Order Function – A system that tracks and stores the details of all Maintenance related activities and costs, both Planned and unplanned
Create, Track, Preview, Print or analyze various Work Order types to include:
- Single Craft Work Orders
- Multi Craft Work Orders or Projects, Major Routine Maintenance (Turnarounds)
- Preventive Maintenance work orders
- Breakdown Maintenance work orders
Track Work orders by the following
- Work Type (Mechanical, Electrical, civil etc.)
- Work Category (safety, legal, environmental)
- Work Priority (normal, important, Urgent)
- Work Order Fault codes and description
Track labor rates, hours, External contractor services and equipment, and material used.
Track all costs associated with Equipment or Entity.
Group Single Task WO to create multi-task WO (Project)
Maintenance Reports, KPi’s and Dashboards – A comprehensive system of Maintenance and cost reports presented in multiple formats including KPI Dashboard formats.
Report types include:
- Work Orders
- PM compliance
- Overdue PMs
- Fault Reports and analysis
- Internal and External Labor, Material, Mobile Equipment reports
- External Services Report
- Cost details and cost summary reports
Maintenance reports can be further classified by:
Date range, Location, Supervisor, Equipment, Equipment Type, Parent, Work type, Maintenance Type, Work Status, Project, or Service Provider.